Udržitelnost ve Skupině ČEZ

Budujeme energetiku, která je spolehlivá, cenově dostupná a přátelská k lidem i k životnímu prostředí. Hledáme a nabízíme ta nejlepší technologická řešení, která pomohou domácnostem být energeticky soběstačné a úsporné, firmám snížit jejich uhlíkovou stopu a komunitám vytvářet chytrá, udržitelná města a obce. Věříme, že vzájemnou spoluprací dokážeme vytvořit novou éru udržitelné energetiky. Jsme ČEZ – Čistá energie zítřka.
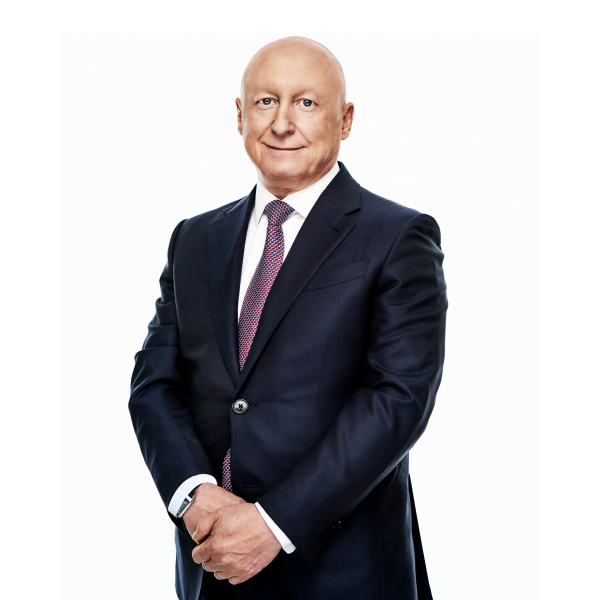
Daniel Beneš
předseda představenstva a generální ředitel ČEZ, a. s.
Výroční finanční zpráva 2024
Stáhněte si naši nejnovější Výroční finanční zprávu 2024
Úspěchy
NovinkyVíce
23/05/2025
Další krok v posilování energetické bezpečnosti. ČEZ se poprvé postaral o přepravu LNG tankeru přes oceánGovernance
Environmental
22/05/2025
V Mělníku vznikne největší paroplynový teplárenský zdroj v ČeskuEnvironmental
21/05/2025
ČEZ modernizuje nejúčinnější českou přečerpávací elektrárnu. Do Dalešic letos investuje 113 milionů korunGovernance
Environmental
17/05/2025
Modernizace za 400 milionu korun startuje. Horní nádrž Dlouhých strání dostane „opalovací krém“Governance
Environmental